Высокотемпературные смазки. Обзор известных материалов
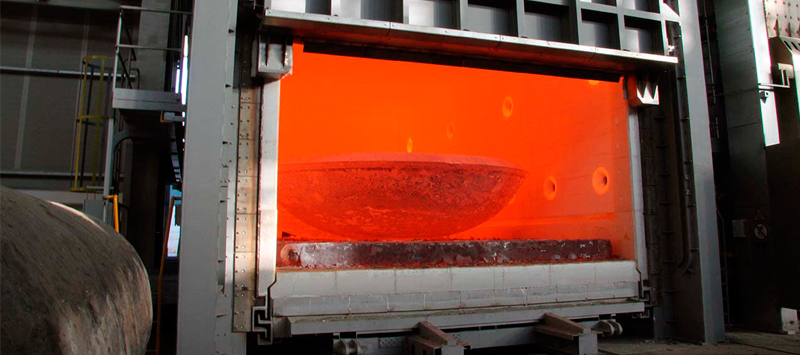
К высокотемпературным, или термостойким, относят те смазочные материалы, которые способны выполнять заявленные функции при температурах, превышающих +150 °С.
- Чем они отличаются от традиционных смазок и какие требования выполняют?
- Где применяются термостойкие составы и как выбрать лучший из них?
На эти и другие вопросы ответим в статье.
Для начала представим рейтинг наиболее популярных высокотемпературных смазок.
Мы выбрали 4 наиболее известных состава и проанализировали комплекс их свойств.
Преимущества высокотемпературных смазок
В отличие от обычных смазок, высокотемпературные при нагревании не плавятся и не вытекают из узлов. Для сравнения – кальциевые составы теряют смазочную способность и пластичную структуру уже при +80 °С, литиевые – при +130 °С. При более интенсивном нагреве они коксуются, выгорают, высыхают.
Термостойкие смазки отлично работают в гораздо более широком температурном диапазоне. Большинство из них выдерживают до +250...+300 °С, а некоторые – до +1500 °С.
Высокотемпературные свойства смазок достигаются путем использования синтетических базовых компонентов, комплексных загустителей (например, фторопласта), специальных присадок.
Некоторые термостойкие материалы имеют двойной механизм смазывания. До достижения определенных температур они действуют как традиционные смазки, а при дальнейшем нагреве – как твердые.
Применение специальных компонентов и технологий при изготовлении высокотемпературных смазок существенно увеличивает их стоимость, поэтому их нецелесообразно применять в обычных условиях – там, где могут работать стандартные материалы.
Жаростойкие составы наиболее эффективны лишь в тех узлах, которые постоянно или с определенной периодичностью подвергаются воздействию высоких температур.
Требования к термостойким смазкам, как и к традиционным, определяются конкретными условиями их применения.
Подавляющая часть промышленного высокотемпературного оборудования работает при +200... +250 °С, поэтому верхняя граница термостойких смазок должна включать эти значения. В местах соприкосновения трущихся деталей они должны обеспечивать устойчивый смазочный слой, предотвращающий непосредственный контакт поверхностей.
В конструкции большинства современных механизмов используются детали из пластмасс и эластомеров. Поэтому жаростойкие сервисные материалы должны быть совместимы не только с металлами, но и с этими материалами.
Виды высокотемпературных смазок
По консистенции высокотемпературные смазки можно разделить на несколько основных типов:
- Жидкие (масла)
- Пластичные
- Пасты
- Антифрикционные покрытия
Термостойкие масла изготавливаются на основе нефтяных или синтетических (чаще силиконовых) масел, в составе могут содержать специальные присадки.
Пасты включают частицы твердосмазочных веществ, в большой концентрации диспергированные в масле. Под действием нагрузок или высоких температур жидкие масла выдавливаются из зон трения или разрушаются, твердые же смазки заполняют микронеровности поверхностей и сглаживают их.
Антифрикционные покрытия также состоят из твердых частиц. Однако диспергированы они не в масле, а в специальном связующем веществе органической или неорганической природы. После нанесения это вещество отверждается, удерживая твердые смазки на защищаемой поверхности. Большинство АФП способны выдерживать колоссальные нагрузки и температуры.
Пластичные смазки используются для подшипников и других деталей, смазывание которых жидкими материалами не предусмотрено (например, узлов ходовой части или тормозных механизмов транспортных средств, некоторых элементов промышленного оборудования).
Термостойкие пластичные смазки различаются по виду загустителя. Натриевые сохраняют свои свойства при температурах до +200 °С, однако не могут применяться в узлах, контактирующих с водой. В настоящее время такие материалы используются очень редко.
Смазки на основе кальциевого комплекса эксплуатируются при тех же температурах, что и натриевые (до +200 °С), не смываются водой, доступны по цене. Сегодня они нашли широкое применение практически во всех сферах производства. Самые известные кальциевые смазки – УНИОЛ 2М/1, ВНИИНП 207, ВНИИНП 214 и др.
Комплексные кальциевые смазки изготавливаются с использованием как нефтяных, так и синтетических базовых масел. Например, ЦИАТИМ 221С – это высокотемпературная силиконовая смазка.
Кальциевые, силиконовые, полимерные, графитовые и другие высокотемпературные материалы широко используются на предприятиях химической, энергетической, нефтеперерабатывающей, пищевой, металлургической и других видов промышленности, при обслуживании автомобилей.
Ниже приведены некоторые примеры применения термостойких смазок:
- Подшипники печей, сушилок и другого высокотемпературного оборудования
- Резьбовые соединения экструдеров
- Узлы пищевого оборудования
- Узлы оборудования по производству и переработке полимеров
- Подшипники вентиляторов
- Подшипники насосов по перекачке химически агрессивных сред
- Подшипники обжиговых вагонеток, тележек печей
- Ступичные подшипники
- Суппорты дисковых тормозов
- Электрические узлы автомобилей
- Форсунки дизельных двигателей
- Резьбовые соединения выхлопной трубы
- Термовалы принтеров
- Узлы энергетической запорной арматуры
- Конвейерные цепи
Следует помнить, что только правильный подбор высокотемпературных смазок с учетом особенностей каждого конкретного применения способен повысить срок службы механизма и значительно увеличить интервал между его обслуживанием.