Твердая смазка: основные компоненты и отличия от традиционных материалов
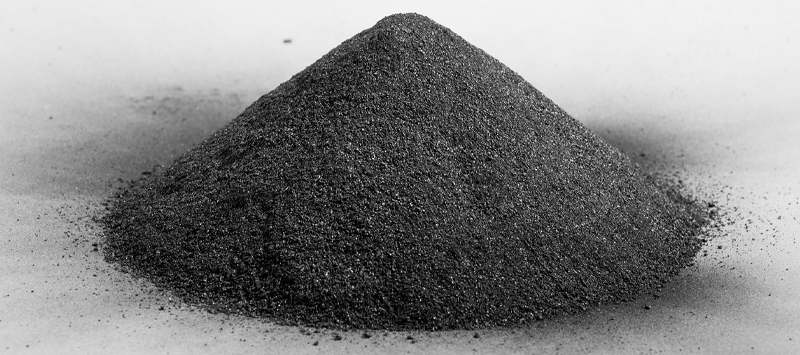
- Твердая смазка: почему возникла необходимость ее применения?
- Основные компоненты твердой смазки и способы ее нанесения
- Антифрикционные покрытия как наиболее эффективный способ применения твердосмазочных материалов
Твердая смазка: почему возникла необходимость ее применения?
Твердая смазка – это порошкообразные или пленочные материалы, которые применяются на сопряженных поверхностях для снижения их трения и износа.
Многие современные материалы, реализующие технологию твердой смазки, обладают также антикоррозионными, противозадирными, антиадгезионными и другими дополнительными свойствами.
Необходимость в поиске смазочных материалов нежидкой формы появилась вследствие развития узлов и механизмов техники, их эксплуатации в экстремальных условиях.
Многочисленные отказы оборудования в вакууме, при высоких или низких температурах, при высоких нагрузках и скоростях скольжения стали причиной поиска более эффективных способов снижения трения и износа узлов.
В некоторых условиях традиционные смазочные материалы крайне быстро теряют свои свойства и требуют постоянного обновления, а во многих, например, в вакууме, они вовсе не могут быть применены.
Одним из современных требований к смазочным материалам является их экологичность и безопасность. Традиционные смазки выделяют токсичные испарения, загрязняют окружающую среду и несут опасность для здоровья людей.
Твердые же составы не испаряются и не оказывают вреда окружающим системам. Кроме того, они демонстрируют крайне низкий коэффициент трения и длительный срок службы.
Основные компоненты твердой смазки и способы ее нанесения
Смазочные свойства твердых материалов, например, графита, были известны задолго до появления необходимости в их широком применении. Именно графит стал первым твердым веществом, которое стали изучать и использовать для снижения трения в экстремальных условиях.
Тестирования показали, что во влажной среде графит демонстрирует коэффициент трения 0,03, а при отсутствии влаги этот параметр возрастает. Поэтому были сделаны выводы о том, что в условиях вакуума этот материал мало эффективен.
Открытый позднее дисульфид молибдена стал находкой для проектировщиков космической техники. Его коэффициент трения в вакууме составил 0,02. Он сохраняет работоспособность при высоких температурах и в контакте с агрессивными средами, однако во влажной среде свойства вещества ухудшаются.
Высокие эксплуатационные свойства показывает комбинированное использование графита и дисульфида молибдена в строго определенных пропорциях.
Кроме веществ слоистой кристаллической структуры антифрикционные свойства показывают и некоторые полимеры, например, политетрафторэтилен. Он устойчив к влиянию химически агрессивных составов, имеет низкий коэффициент трения (0,02 – 0,05), работает в широком диапазоне температур.
Способы применения твердых смазочных материалов:
- Порошкообразная форма – простого нанесения порошков твердых смазок на поверхности трения в современных условиях недостаточно, так как они непрочно удерживаются на месте применения
- Введение в состав пластичных и жидких смазок – твердые компоненты добавляются в состав смазочных материалов для улучшения их свойств. Однако в экстремальных условиях эксплуатации такие комбинации остаются неэффективными, как и смазочные составы без добавления твердых веществ
- Напыление – образование на деталях тонкой пленки, которая не имеет длительного ресурса
- Интеграция твердых веществ в поверхность трения – создание суспензий порошков твердых смазок, связующих веществ и растворителей
Последний способ позволяет создать слой, обладающий длительным ресурсом. Этот метод реализуется через разработку антифрикционных покрытий.
Антифрикционные покрытия как наиболее эффективный способ применения твердосмазочных материалов
Покрытия на основе твердых смазочных материалов в России выпускает компания «Моденжи».
Антифрикционные твердосмазочные покрытия MODENGY – это материалы, представляющие собой суспензии порошков твердых смазок, органических / неорганических связующих и растворителей.
Они наносятся на подготовленные (очищенные и обезжиренные) поверхности методами окрашивания и полимеризуются в печи либо при комнатной температуре.
В процессе полимеризации растворитель испаряется и на деталях остается прочно сцепленная с поверхностью матрица связующего вещества, заполненная частицами твердых смазок.
Характеристики покрытий:
- Низкий коэффициент трения – от 0,03
- Широкий диапазон температур – в линейке MODENGY есть как материалы, работающие при крайне низких температурах, так и покрытия для эксплуатации при сильном нагреве
- Химостойкость
- Работоспособность в вакууме, в условиях радиации и других экстремальных режимах эксплуатации
- Сухая текстура
- Эстетичный внешний вид
- Малая толщина – от 15 до 30 микрометров
- Антикоррозионные свойства – до 1000 часов защиты от коррозии по результатам ускоренных испытаний в соляном тумане по стандарту ISO 9227
- Несущая способность до 3000 Мпа, противозадирные свойства
- Антиадгезионные и гидрофобные свойства
- Отсутствие токсичных испарений
Сегодня твердая смазка благодаря своим свойствам распространена практически во всех отраслях производства: в машиностроении, роботостроении, космической отрасли, на производствах полимерных изделий, нефтегазовых предприятиях, в атомной энергетике и т.д. Ее используют не только для защиты деталей в экстремальных условиях эксплуатации, но и в качестве более эффективной и долговременной замены пластичным и жидким смазкам.