Твердая смазка: характеристики и обзор применения
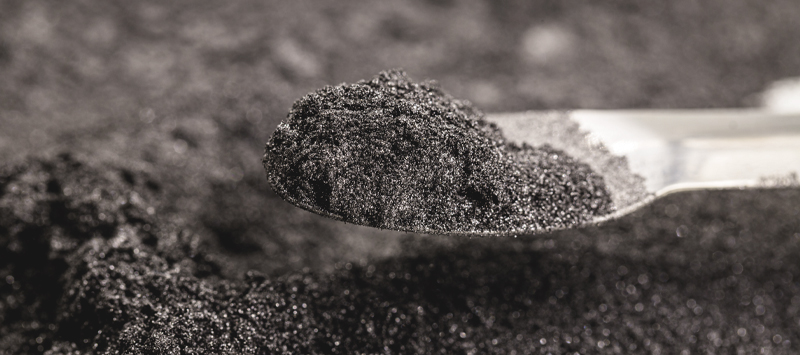
- Что из себя представляет твердая смазка?
- Дисульфидмолибденовая и графитовая паста
- Покрытия, реализующие технологию твердой смазки
Что из себя представляет твердая смазка?
По мере развития технологий и техники, выхода человека в космос, появления атомной энергетики и необходимости эксплуатации оборудования в экстремальных условиях, остро встал вопрос замены известных пластичных смазок на другие антифрикционные материалы.
В условиях высоких температур, нагрузок, контактных давлений, низких скоростей скольжения, вакуума, под водой жидкие компоненты смазок выгорают, испаряются, вытесняются или по другим причинам быстро теряют свою работоспособность.
В поисках новых видов смазочных материалов ученые обратились к твердым веществам (термопластическим полимерам, минералам, мягким металлам и другим), которые в виде мелкодисперсного порошка обладают очень низким коэффициент трения, при этом могут работать в самых суровых условиях.
Тведосмазочные вещества создают на деталях смазочный слой с малой прочностью на сдвиг, при этом они хорошо выдерживают нагрузку, направленную перпендикулярно к их атомным плоскостям.
Это значит, что слои твердой смазки легко скользят друг относительно друга, чем обусловлен малый коэффициент трения.
В процессе трения порошки твердых смазок заполняют микронеровности обработанной поверхности и формируют смазочную пленку. Это и есть твердая смазка.
Она работает аналогично граничному слою смазочной жидкости, обладает малой прочностью на сдвиг и очень высокой несущей способностью.
Твердосмазочных компонентов достаточно много. Это дисульфид молибдена, графит, политетрафторэтилен, дисульфид вольфрама, порошки мягких металлов – медь, алюминий, индий и другие.
Причем прочность на сдвиг и коэффициент трения у металлов намного выше, чем у остальных перечисленных веществ. Поэтому смазкой их называют условно, используя в составе смазочных материалов за высокую работоспособность в экстремальных условиях.
Твердые смазочные вещества могут использоваться самостоятельно в виде порошков. Получило широкое распространение их добавление в жидкие и пластичные смазки для увеличения их несущей способности и обеспечения антиаварийной смазки при опасности потери работоспособности жидких компонентов.
Для повышения адгезии и удобства нанесения твердые смазочные порошки смешиваются с маслом – получаются твердосмазочные пасты. В состав также могут входить функциональные добавки при необходимости. Масло создает своеобразный каркас, в котором удерживаются мелкодисперсные частицы.
Пасты способны работать в тех условиях, где пластичные и жидкие смазки теряют работоспособность – при высокой или очень низкой температуре, сверхвысоких нагрузках, низких скоростях скольжения.
Наибольшее распространение для создания твердосмазочных паст получили графит и дисульфид молибдена. И дисульфидмолибденовая, и графитовая паста предназначены для работы в высоконагруженных узлах трения.
Дисульфидмолибденовая и графитовая паста
Дисульфид молибдена (MoS2) и графит (C) являются веществами слоистой структуры с малой прочностью на сдвиг.
Дисульфид молибдена отличается очень высокой несущей способностью (2800 МПа), низким коэффициентом трения, химической стабильностью, стойкостью к кислотам и щелочам, радиации. Он является самым распространенным материалом для работы в вакууме, где демонстрирует крайне низкий коэффициент трения и высокую термостойкость.
Графит характеризуется низким коэффициентом трения (как правило, выше, чем у MoS2), электропроводностью, химической стабильностью, термостойкостью, радиационной инертностью. Наилучшие показатели демонстрирует при функционировании во влажной среде, при отсутствии влаги коэффициент трения материала повышается.
Данные вещества эффективны по отдельности, однако нередко работают вместе, демонстрируя синергетический эффект.
Например, на основе дисульфида молибдена с добавлением графита изготовлена твердосмазочная паста MODENGY 4002.
Характеристики пасты:
- Термостойкость до +450 °С и до +600 °С при ограниченном доступе воздуха
- Устойчивость к смыванию
- Удобство нанесения
- Малый коэффициент трения (0,05-0,08 в паре трения «сталь-сталь»)
- Повышенная несущая способность
- Противозадирные свойства
- Способность обеспечивать плавное движение без скачков и рывков
Твердосмазочная паста имеет очень широкую область применения. Это тяжелонагруженные тихоходные узлы с парами трения металл-металл, резьбовые соединения, ходовые винты, зубчатые зацепления, шлицы, посадки с натягом, плашки и метчики для нарезания резьбы и многие другие механизмы.
Паста минимизирует трение, защищает от фреттинг-коррозии, предотвращает задиры, закусывания, прикипание, обеспечивает легкий монтаж и демонтаж даже после длительной эксплуатации в экстремальных условиях.
Покрытия, реализующие технологию твердой смазки
Наиболее современными материалами, реализующими технологию твердой смазки, являются покрытия с применением твердых смазочных компонентов. Они помогают интегрировать частицы твердой смазки в поверхности трения.
Для этого в состав покрытий помимо высокодисперсных порошков включаются связующие компоненты, например, смолы.
Преимуществом покрытий, которым не может похвастаться ни один из других типов материалов с твердосмазочными компонентами, является очень длительный срок службы.
Если смазки и пасты необходимо обновлять после каждой разборки механизмов, то слой покрытия не нуждается в повторном нанесении и может выступать в качестве ресурсной смазки.
Также их выгодно отличают нетоксичность после отверждения, способность работать в запыленной среде, высокие антикоррозионные свойства, высокая несущая способность, термостойкость, устойчивость к влиянию агрессивных сред.