Испытание покрытия на антикоррозионные свойства
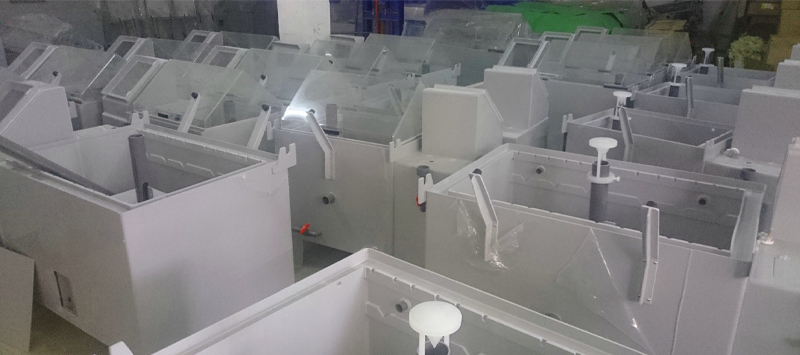
- Для чего проводят испытание покрытий?
- Методы испытания покрытий
- Испытания защитных покрытий в России
Для чего проводят испытание покрытий?
Защитное покрытие – это образованный после нанесения защитных материалов слой, который обладает высокой адгезией к основе и осуществляет функцию по предотвращению повреждения деталей при их эксплуатации в агрессивных условиях.
По химическому составу они подразделяются на металлические и неметаллические.
Металлические покрытия создают слой, осуществляющий анодный или катодный способ защиты деталей от разрушения под воздействием негативных факторов окружающей среды.
Катодные покрытия обеспечивают только механическую защиту и сохраняют свои свойства лишь в случае сохранения целостности и большой толщины слоя.
Анодные покрытия более распространены за счет своей стойкости к различным механическим повреждениям. Даже при возникновении сколов они предотвращают образование и распространение очагов коррозии.
К неметаллическим защитным покрытиям относят, например, лакокрасочные и полимерные материалы.
С целью определения времени сохранения противокоррозионных свойств покрытий и сравнения нескольких материалов проводят испытания. Они могут осуществляться в нормальном режиме эксплуатации деталей, а также в лабораторных условиях.
Методы испытания покрытий
Наиболее надежным способом определения времени сохранения антикоррозионных свойств покрытий являются натурные исследования. Они заключаются в наблюдении за поведением защитного слоя в реальных условиях эксплуатации деталей, на которые они нанесены.
Однако такие тестирования могут продлиться не один год. Поэтому были разработаны методы испытания покрытий за короткий срок – исследования в агрессивной среде или в климатической камере.
Они заключаются в искусственном воссоздании условий, в которых работоспособность и сохранение защитных свойств покрытий ставится под сомнение.
Климатические испытания на коррозию заключаются в помещении образцов в испытательный блок оборудования, где воссоздаются и усиливаются дневные или сезонные колебания климата.
В них меняется температура, влажность и другие условиях, характерные для нормальной эксплуатации деталей.
Уменьшение времени на получение результатов достигается за счет интенсификации влияния негативных факторов окружающей среды, поэтому при прогнозировании ресурса защитных покрытий с учетом данных климатических испытаний могут наблюдаться погрешности.
Еще одним способом ускоренных испытаний является воздействие на объекты агрессивной среды – концентрированного раствора вещества, стимулирующего развитие коррозии на образцах.
Наиболее часто испытания проводят в камерах соляного тумана. Соль является одним из наиболее распространенных веществ, оказывающих негативное воздействие на оборудование, металлические конструкции и другие компоненты.
Раствор хлорида натрия распыляется по испытательной камере с размещенными образцами через определенные промежутки времени, оказывая агрессивное воздействие на покрытия.
С помощью испытаний сравнивают защитные характеристики покрытий. Такой метод не может применяться для прогнозирования эксплуатационных свойств материалов и срока сохранения противокоррозионных свойств покрытий.
Испытания защитных покрытий в России
Испытания защитных покрытий, а также смазочных и консервационных составов и других материалов проводятся в лабораториях, оснащенных камерами соляного тумана.
Процесс испытаний обязательно должен соответствовать российскому или международному стандарту в области осуществления исследований на определение коррозионной стойкости материалов, противокоррозионных свойств покрытий и других составов на лабораторных установках.
Услугу по проведению испытаний защитных покрытий и других составов оказывает российская компания «Моденжи», специализирующаяся на производстве материалов, реализующих технологию твердой смазки в виде твердосмазочных покрытий.
Инженерный центр MODENGY оборудован испытательной установкой, позволяющей тестировать защитные покрытия в соляном, кислотном, щелочном тумане, а также проводить циклические коррозионные испытания.
Последние заключаются в смене режимов работы камеры: распыления агрессивной среды, сушки, колебания влажности и других условий в зависимости от особенностей и назначения испытаний.
Тестирования осуществляются согласно международному стандарту ISO 9227.
Этапы испытаний в камере с агрессивной средой:
- Сбор данных для составления технического задания, выбор метода тестирования, разработка подробного плана эксперимента
- Наполнение соляным раствором предназначенного для этого бака
- Настройка всех параметров эксперимента: температура и влажность в камере, интенсивность и периодичность распыления раствора и тд
- Подготовка образцов к тестированию: очистка и обезжиривание поверхности, нанесение защитных покрытий, проверка качества покрытия
- Регистрация дефектов поверхности образцов до начала испытаний
- Включение испытательной установки
- Размещение образцов в камере следуя правилам, указанным в стандарте
- Периодический контроль и фиксация изменения состояния защитного покрытия, регистрация времени появления первых очагов коррозии на образцах
- Окончание эксперимента, анализ полученных данных
- Составление отчетной документации
После проведения эксперимента заказчику предоставляется отчетная документация, содержащая рекомендации специалистов по выбору защитного покрытия. Все права на результаты, отраженные в отчете, также передаются клиенту.
Испытание покрытий в агрессивных условиях позволяет получить сравнительные данные о характеристиках материалов с целью подбора наилучшего решения для конкретных условий эксплуатации.