Антифрикционные покрытия в металлургии. Применение твердой смазки для повышения ресурса оборудования
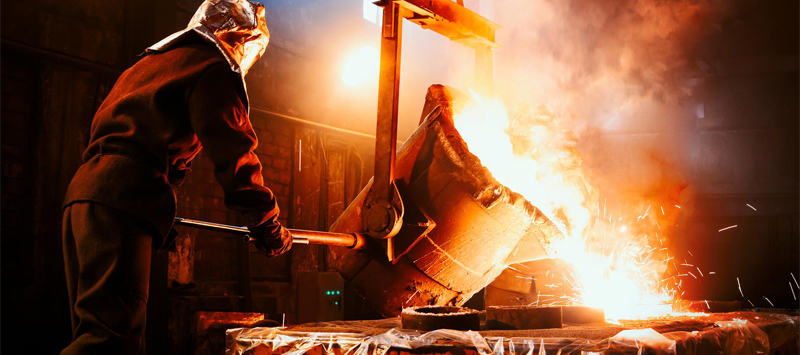
- Актуальность использования технологии твердой смазки на металлургических предприятиях
- Опыт применения антифрикционных покрытий в металлургии
Актуальность использования технологии твердой смазки на металлургических предприятиях
Металлургия относится к одной из самых сложных отраслей производства. И оборудование для осуществления операций по изготовлению изделий из металла работают в тяжелых условиях.
Среди них воздействие высоких температур при работе с металлическими расплавами, экстремальные нагрузки и давления, неблагоприятные факторы окружающей среды.
Чтобы обеспечить надежное и длительное функционирования металлургического оборудования, применения традиционных смазочных составов становится недостаточно.
Сегодня во всех отраслях промышленности, в том числе и металлургической, получают все большее распространение твердосмазочные покрытия.
Они наносятся на детали методом распыления и после цикла отверждения формируют тонкую пленку, обладающую высокими эксплуатационными свойствами: низким коэффициентом трения, высокими противозадирными свойствами и несущей способностью, химостойкостью, работоспособностью как в экстремально высоких, так и криогенных температурах, противокоррозионными свойствами.
Рассмотрим, в каких конкретно узлах оборудования металлургической промышленности уже применяются твердосмазочные покрытия и как использование твердой смазки позволяет оптимизировать процесс производства.
Опыт применения антифрикционных покрытий в металлургии
Для производства изделий из металла необходимо добыть руду из недр земли. На добывающих предприятиях используется огромный комплекс оборудования.
На извлекательных фабриках для измельчения руды применяется дробильное оборудование. В процессе его сборки и настройки помогает нанесение антифрикционного твердосмазочного покрытия MODENGY 1003.
Материал на основе дисульфида молибдена и графита наносится на упорную резьбу дробилок для предотвращения задиров и закусываний резьбы при скручивании элементов конструкции.
Обычные смазки не могут выдержать такие высокие нагрузки при медленном скольжении – смазочная пленка разрушается при больших контактных давлениях, и сопряженные поверхности начинают схватываться.
Покрытие, обладающее высокой несущей способностью и отличными противозадирными свойствами, эффективно устраняет проблему заедания и закусывания резьбы при сборке крупногабаритных деталей.
Основной проблемой при литье металлов и сплавов является прилипание расплавов к стенкам стальных форм. Из-за этого усложняется извлечение готовых изделий, ухудшается качество их поверхности – требуется дополнительная механическая обработка, а также значительно снижается срок службы формообразующих элементов.
Для предотвращения прилипания расплавленных металлов и сплавов необходимо применение покрытий с высокими антиадгезионными свойствами, которые выдерживают влияние температуры расплава.
На формах для литья металлов и сплавов используются антиадгезионные покрытия MODENGY 1007 и MODENGY 1054. Последнее обладает особо высокой термостойкостью (до +650 °С). Оно предотвращает прямой контакт расплавленного металла и формы, предотвращая их прилипание.
Высокотемпературное покрытие применяется и на элементах роботизированных комплексов для сбора отходов горячего цинкования.
На ковши, которые опускаются в ванну цинкования, наносится MODENGY 1054 для предотвращения прилипания к ним цинконаполненных отходов. Покрытие эффективно работает в условиях высокой температуры, падения расплавленных капель, загазованности воздуха.
В процессе редуцирования металлов эффективно применение антифрикционного покрытия MODENGY 1001. Разделительный слой предотвращает появление дефектов на заготовках в процессе их пластической деформации – задиров и шероховатостей.
Этот же материал применяется на валах прокатных клетей для предотвращения «залипания» на них бронзовых втулок. Благодаря нанесению покрытия процесс запрессовки и распрессовки становится стабильным, а срок службы оборудования повышается.
Холодная штамповка металлов осуществляется с большой скоростью. Направляющие колонки и втулки штампов испытывают высокое трение и повреждаются, а также подвергаются коррозионному разрушению.
Для повышения плавности работы и увеличения ресурса на направляющие детали наносится антифрикционное твердосмазочное покрытие MODENGY 1005 с высокой несущей способностью, износостойкостью и отличными антикоррозионными свойствами.
Для холодной штамповки высоколегированных сталей используется покрытие MODENGY 1020 на основе синтетического воска.
Оно показало наилучшие противоизносные, противозадирные и антифрикционные свойства в процессе трибологических испытаний разделительных покрытий для холодной штамповки, в которых участвовали и успешно зарекомендовавшие себя импортные материалы.
Кроме антифрикционных покрытий технологию твердой смазки реализуют и твердосмазочные пасты. Они содержат большую концентрацию порошков твердой смазки, распределенных в базовом масле. В отличие от покрытий, пасты легче наносятся и не требуют соблюдения режимов отверждения.
Твердосмазочная паста MODENGY 4002 на основе дисульфида молибдена наносится на подшипники и направляющие скольжения, цепные передачи подъемников правильно-отрезных станков.
Она была испытана в оборудовании цехов горячего цинкования и показала высокую термостойкость, отличные антифрикционные и противоизносные свойства.
Твердосмазочные материалы обеспечивают обработанным поверхностям особый комплекс триботехнических и эксплуатационных свойств, что позволяет повышать эффективность и срок службы оборудования металлургических предприятий, работающего в экстремальных условиях эксплуатации.